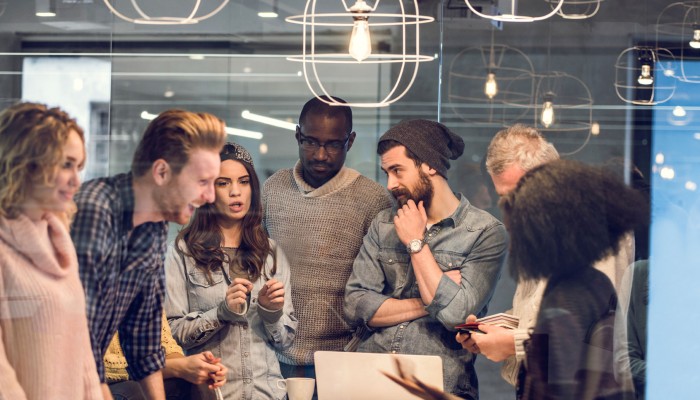
We’ve been hearing the ominous warnings for years now that the average age of the industrial workforce is creeping ever higher and the knowledge gap between experienced and new workers is growing larger every year. Guess what? It’s true! The good news is that at last check, the sky is not falling. Factory floors and machinery are not empty, void of workers to operate them. However, industry is indeed suffering with how to best retain the knowledge that is escaping as experienced workers waltz into the metaphorical sunset. Additionally, companies are grappling with how to best teach a younger demographic – with very different values and motivation – the entire knowledgebase that is required to be effective operators, maintenance personnel and engineers in a modern industrial setting.
To put it bluntly: How do we teach those pesky millennials – raised on computers, gaming consoles, the
In the U.S., by 2030, Millennials will likely outnumber baby boomers 78 to 56 million. – Boston Consulting Group
internet, and social media – how to develop the situational awareness required to operate and maintain complex industrial processes safely and effectively? There is no single “silver bullet” to answer that question. It comes
in a variety of ways, each as unique and varied as the operation, culture, and resources of the multitudinous manufacturing and production companies. However, one often dismissed consideration in this issue is how the control system and, more specifically, the human machine interface (HMI) can be used to help bridge the experience gap.
It’s no secret that industry failed miserably at developing graphical interfaces for distributed control systems (DCS) and related technologies in decades past. Engineers and programmers developed HMI screens to visually mimic the plant floor and related machinery. Hey, it seemed like a good idea at the time! Unfortunately, few (if any) of us were knowledgeable of human cognitive psychology or human factors engineering. We found ourselves with fancy new computer software and graphics technology loaded with cool objects and pretty colors and we started having fun. If we’re being honest, our goal wasn’t to develop situational awareness; it was to impress and entertain ourselves and others at how clever we could be. Of course, engineers being terribly unimaginative, it didn’t take long before duplicating piping and instrumentation diagrams (P&ID) and process flow diagrams (PFD) became the norm in most industries.
I’m going to go out on a limb and guess that you probably have a smart phone in your pocket right now. Open it up and take a look at some of the apps that you have loaded. Next, open your web browser and take a look at the trend that many web sites seem to be following. Do you see a common theme? Dashboard concepts are widely used. Pages are svelte, with minimalistic layouts and intuitive navigation. You might even call them simplistic. That’s not an accident. The software industry is light years ahead of process control and manufacturing systems. They have taken the time to understand and apply visual perception, cognition, and other human factors. Modern software appears minimalist because it works! Simplistic or minimalistic does not have to mean dumbed down. Information – even large amounts of it – can be communicated clearly with great success when we are thoughtful and purposeful in our HMI design.
So, what does this have to do with the knowledge gap that exists in industry? Remember those pesky millennials? What visual design style and principles do you think they’ve grown up with and become accustomed to? Bingo! The ones you see today in your smart phone apps and web sites. It might come as a surprise, but despite their growing up saturated with video games, social media, and reality television, young people joining our workforce actually have the capacity to learn the principles of manufacturing, production and process control, and do it safely. Just like it took us years though, it won’t happen overnight. However, putting thought into our HMI designs and assessing the needs of the user – particularly the up and comers – we can help shorten the learning curve.
While not purposed to be a comprehensive design manual, the recently released ANSI/ISA-101 Human Machine Interfaces for Process Automation Systems is a huge step in the right direction for industry. It “…addresses the philosophy, design, implementation, operation, and maintenance of HMI’s…, including multiple work processes throughout the HMI lifecycle.” If followed, users can get a firm foothold on systemizing a framework for managing all aspects of their facility HMIs. If good training is coupled with sound design principles for displaying information, you are likely to have HMIs that promote safe, effective, and efficient process control, even as the face of the workface is changing.
Interested in taking steps toward improvement? If so, ask yourself these 3 questions:
- Do I have a working knowledge of ANSI/ISA-101 Human Machine Interfaces for Process Automation Systems?
- Does my facility have an HMI Philosophy and Style Guide?
- Is my HMI an effective tool to help manage abnormal process conditions?
If you answered ‘No’ to any one of these questions, you likely have room for improvement in your facility. If you need help getting started with an HMI improvement project, contact SYCON International to see if you qualify to have a subject matter expert review, assess, and provide you a FREE written report on your current HMI configuration and work practices.
Marcus C. Dudoit – Partner & Sr. Consultant